Additive Molding
Innovativer Ansatz für Additive Werkzeugformen –
Optimierung des Spritzgussprozesses durch smarte Kühlung und neue Fertigungsstrategien
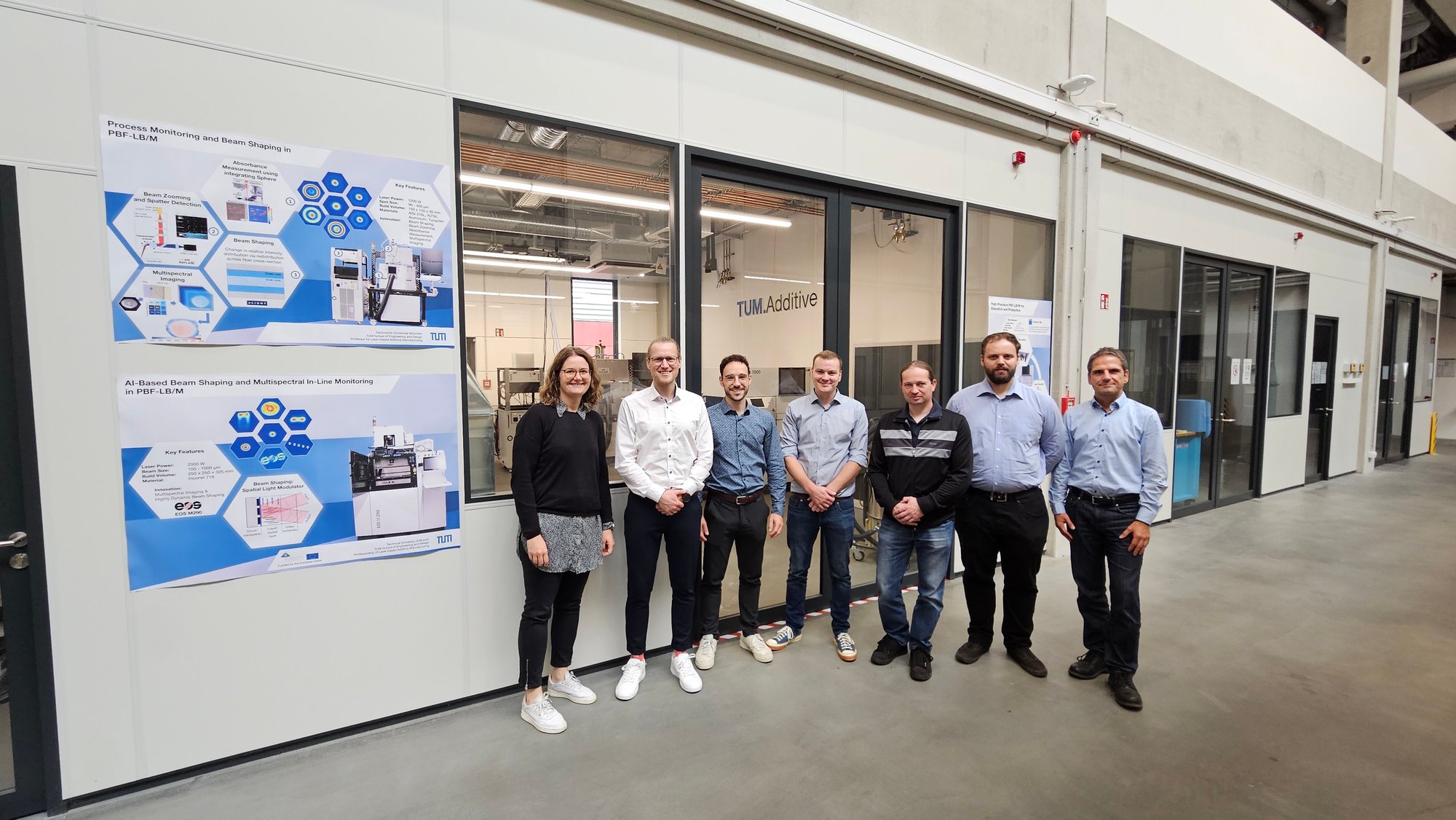
Projektübersicht
Im Rahmen des FuE-Kooperationsprojektes Additive Molding (Fkz. KK5204202LL3) wird ein vollkommen neuer Ansatz zur Herstellung von additiven Werkzeugformen entwickelt, der die gesamte Prozesskette von der additiven Fertigung bis zur fertigen Kunststoffformteilproduktion berücksichtigt. Während in bisherigen Anwendungen die additive Fertigung lediglich als Werkzeugherstellung genutzt wird, erweitert dieses Projekt den Fokus auf das Endprodukt – das Kunststoffformteil – und seine Eigenschaften. Ziel ist es, durch eine optimierte Fertigung und innovative Kühlkanaldesigns die Qualität der Kunststoffteile und den gesamten Spritzgussprozess zu verbessern.
Präzise digitale Evaluierung zur thermischen Optimierung
SIMCON bringt seine Expertise im Bereich der Spritzguss-Simulation ein und entwickelt digitale Evaluierungswerkzeuge, um die Kühlkanalstrukturen der additiv gefertigten Werkzeugeinsätze optimal auf die thermischen Anforderungen abzustimmen. Mit unserer Simulationssoftware CADMOULD leiten fokussieren wir den angepassten Wärmetransfer durch die innovativen Kühlkanalgeometrien, was eine präzise thermische Simulation des Spritzgussprozesses ermöglicht. Dies führt zu einer verbesserten Steuerung der Bauteilmorphologie und optimiert das Endergebnis – die Kunststoffformteile.
Langfristige Perspektive
Das langfristige Ziel dieses Projekts ist es, die Herstellung von Werkzeugen nicht nur für den Optik-Spritzguss durch innovative Kühlkanäle und optimierte Fertigungsprozesse effizienter und nachhaltiger zu gestalten. Mit neuen Ansätzen in der additiven Fertigung und präzisen Simulationslösungen strebt das Projekt eine signifikante Verbesserung der Qualität und Produktivität in der Kunststoffindustrie an.
Projektpartner
Dieses innovative Projekt wird in enger Zusammenarbeit eines hochqualifizierten Konsortiums durchgeführt:
- Technische Universität München (TUM): Entwickelt neue Strategien zur schichtfreien, additiven Fertigung und innovative Kühlkanaldesigns.
- Technische Hochschule Rosenheim (THR): Verantwortlich für die thermische Optimierung und Steuerung der Morphologie der Kunststoffformteile.
- Hans-Hermann Bosch GmbH: Pionier in der Anwendung der PECM-Technologie zur Nachbearbeitung der Werkzeugeinsätze.
Förderkennzeichen
KK5204202LL3Projektträger
AiF Projekt GmbHLaufzeit
01.04.2024-30.09.2027
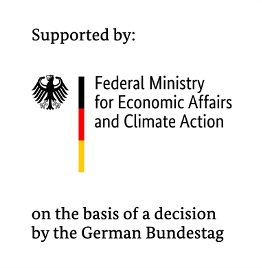