RESEARCH PROJECTS
We create technological progress
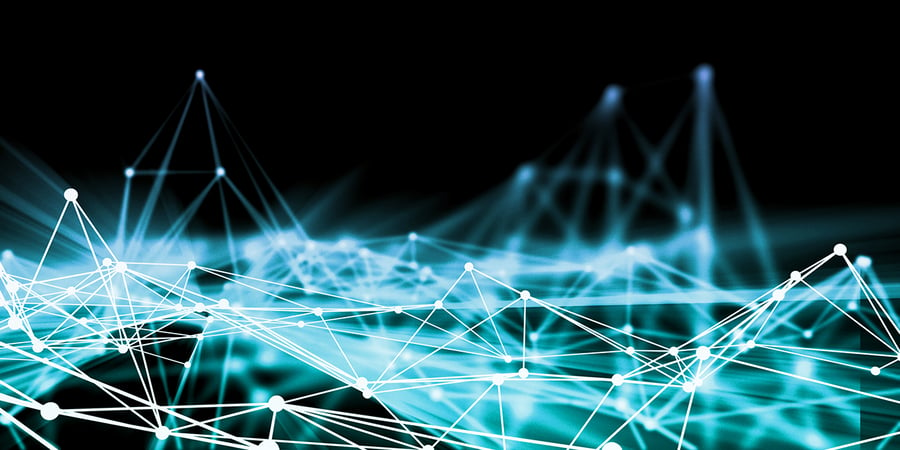
KI-OPTI-PACK
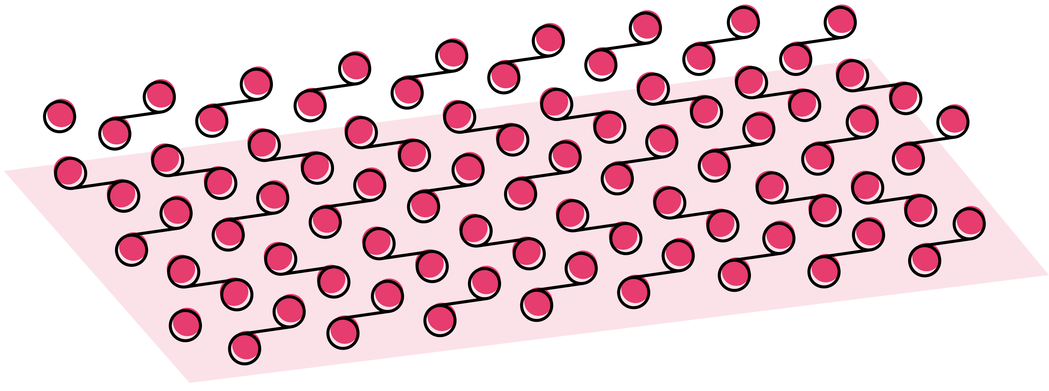
Ki-Opti-pAck
Holistic AI-based optimization of plastic packaging with recycled content.
Artificial intelligence (AI) can help reduce waste and use resources to their full potential. To ensure that this potential can be exploited, AI methods from the entire value chain are being tested in the application hub.
Packaging accounts for the largest share of plastic waste worldwide. Currently, unfortunately, only a small part of the plastic gets back into the cycle as secondary raw material. In the research project "AI Application Hub Plastic Packaging - Sustainable Circular Economy through Artificial Intelligence", AI methods are used to improve the sustainability of plastic packaging.
The two innovation labs KIOpti-Pack (design and production) and K3I-Cycling (closing the loop) are working to close the value chain of plastic packaging.
More information will you'll find here.
Sponsored by
Federal Ministry of Education and Research
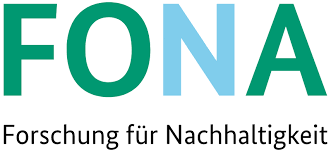
Sponsored by
RESEARCH FOR SUSTAINABILITY
HyTraM
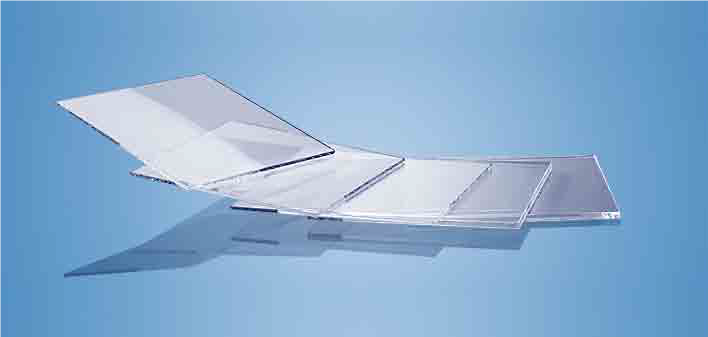
HyTraM
Development of hybrid thermal shock resistant material composites made of transparent materials for innovative functional and design components.
Transparent functional and design components are used for a wide range of applications in medicine, biotechnology/microfluidics, automotive, displays, and lighting technology and are made of either glass or plastic.
In addition to high light transmission, these two materials have specific disadvantages that limit their use. While glass components have a limited variety of shapes, plastic parts offer low scratch resistance, have a low resistance to chemicals, and allow only low operating temperatures and thermal cycling.
Hybrid glass-plastic material composites can overcome these limitations by combining the advantages of the two types of materials. Currently, such compounds are made by bonding, allowing only a few thermal cycling cycles and having low strengths. The adhesive bonding of the two materials by back-injection of the glass component with plastic has been tested to some extent. Still, it requires particular adhesion promoters that are unavailable depending on the compound and is not satisfactory in terms of glass tolerances when inserted into the injection mold.
Using a laser-based joining technique, in which the glass component is first laser-structured and then joined to the plastic part by both laser beam entering and back injection, a hybrid glass-plastic composite with high thermal shock resistance is produced.
Duration
Nov 1, 2018 – Jul 1, 2021
Project sponsor
LeitmarktAgentur.NRW
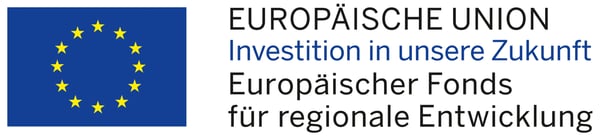
Sponsored by
European Regional Development Fund

Sponsored by
Ministry of Economics NRW
VMAP
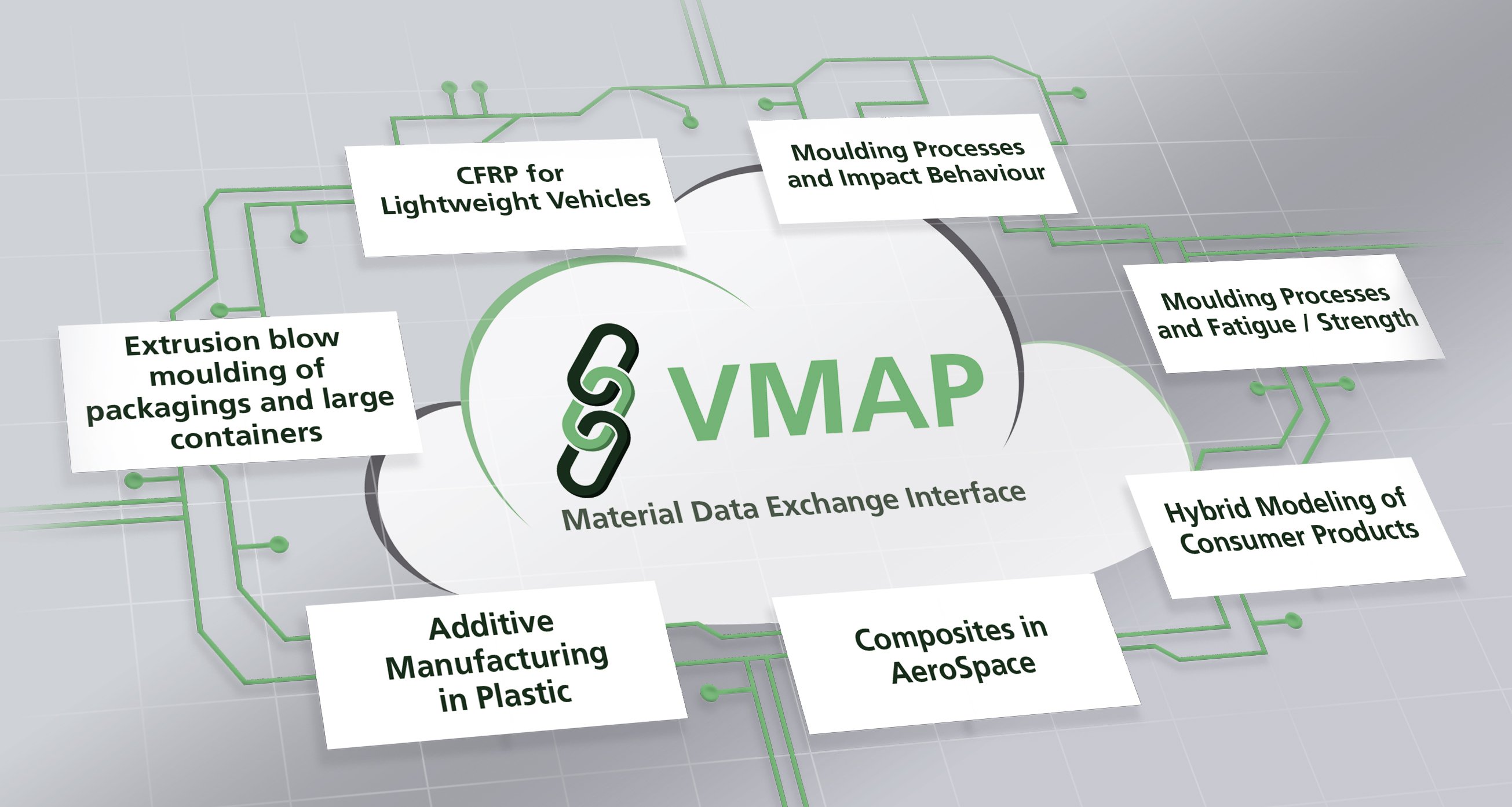
VMAP
Virtual Material Modelling in Manufacturing
The ITEA-VMAP project aims to achieve a shared understanding and interoperable definitions for virtual material models in CAE.
New concepts for a universal material exchange interface for virtual engineering workflows have been created, using industrial use cases from key material domains and representative manufacturing processes.
Challenge accepted
In virtual engineering workflows, there is a lack of software standards, and no agreed-upon standard interface to transfer virtual material information. This causes unnecessary costs and complex manual adjustments, leads to inflexible IT solutions, loss of information, and significant delays in the overall design process. We believe that a standardization of material interfaces in CAE is crucial for all industry segments where material behavior is central to product and process design.
In short, VMAP generates universal concepts and open software interface specifications for exchanging material information in CAE workflows. The concepts created in the VMAP project are now being implemented in a set of software tools. In the project, the benefits of integrated material handling were demonstrated using six industrial use cases from different material categories, manufacturing domains, and industry segments. Software implementation will manifest in the form of advanced CAE tool interfaces and, if necessary, translation tools that follow the open interface specification. VMAP will also implement virtual industry demonstrators for relevant material domains and manufacturing processes and provide best practice guidelines to the community. Establishing an open and vendor-neutral community called the Material Data Exchange Interface Standard will ensure that standardization efforts continue.
Interoperable virtual material models and the seamless transfer of material data history in a CAE workflow enable industry users to develop and produce better products in less time and more efficient manufacturing processes. CAE software developers and vendors can use interface standards to realize additional virtual material models that can be easily integrated into the holistic design, simulation, and optimization workflows. In Europe's future manufacturing market, where materials technology is a crucial enabler, an open software interface standard for virtual material modeling will carry a significant benefit, especially in the fast-growing additive manufacturing market for metals and plastics.
Duration
Sep 1, 2017 - Oct 31, .2020
Project sponsor
Fraunhofer SCAI
Sponsored by
Federal Ministry of Education and Research
Sponsored by
ITEA4
TSchaum + Funktion
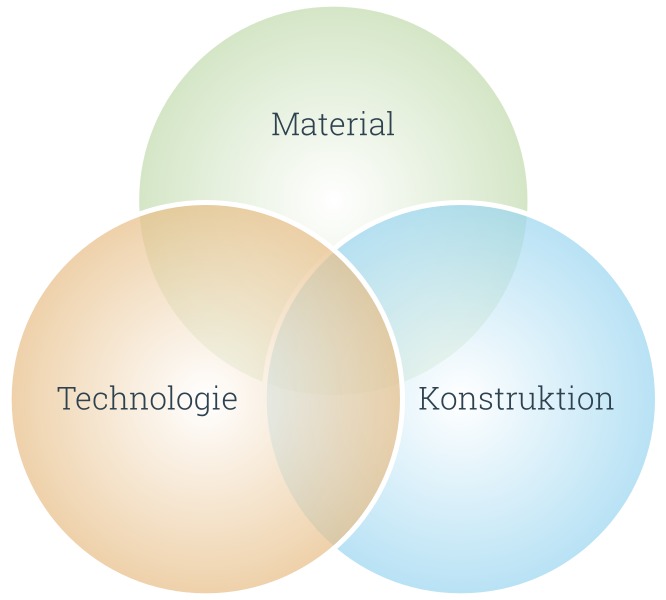
Tfoam + Function
Lightweight construction network
Functional construction methods with thermoplastic foams - this is the heading of the "TSchaum+Funktion" network founded in October 2017 as part of the Central Innovation Program for SMEs (ZIM) under the leadership of Kunststoff-Zentrum in Leipzig gGmbH (KUZ).
ZIM cooperation networks provide small and medium-sized enterprises (SMEs) with a platform for pooling expertise from various industrial sectors. The cooperation facilitates the implementation of the latest developments in science and technology into marketable products. The KUZ acts as a network management institution, coordinating and supporting the collaboration of the partners.
In the "TFaoam +Function" network, new applications are developed based on thermoplastic foam injection molding, in which lightweight components with integrated functionality bring economic and ecological advantages. The way to create innovative solutions is through:
- Combination with other technologies such as sandwich injection molding
- Broadening the range of plastics
- Functional integration, e.g., by combining with inserts, gating elements, functional layers or additives, and
- Replacement of non-thermoplastic foams.
The market demand for competitive lightweight components is high and increasing. Therefore, the increase in know-how in the field of lightweight construction is also of central importance for the competitiveness of SMEs.
Duration
Jul 1,2018 – Sep 30, 2020
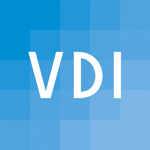
Project sponsor
The Association of German Engineers | VDI
Sponsored by
Federal Ministry of Education and Research
COSIMA

CoSiMa
Connecting simulation and machine to optimize the production process of injection molded parts
The research project "Connecting simulation and machine to optimize the production process of injection molded parts - CoSiMa" (03INT507BA) aims to realize seamless communication between process simulation and injection molding machine.
Together with an international consortium of German and Slovenian companies and the Slovenian research cluster Tecos - Slovenian Tool and Die Development Centre, Celje, Slovenia, a transfer function is being developed to transfer simulation-based setting data records directly to the injection molding machine. Using a Manufacturing Execution System (MES) as a mediator between simulation and machine, it will also be possible to support the operator at the machine in the setting process by providing the simulation results of a relevant process window.
In addition to its content-related activities, the IKV also coordinates the successful international cooperation within the consortium. ARBURG is driving the machine-side development of the necessary interfaces and the machine control system, while GRP provides the infrastructure for data handling. Simcon is pushing the simulation-side interface and the stored material models. TECOS coordinates the work of the Slovenian partners and considers mold-dependent influencing factors, while practical tests are carried out at the partners KOLEKTOR and TEHNOMAT.
Duration
Jun 1, 2018 - Sep 30, 2021
Project sponsor
Project Management Jülich | PTJ
Sponsored by
Federal Ministry of Education and Research
Would you like to know more,
or are you looking for a project partner?
Get in touch at solutions@simcon.com.